САМОЛЕТЫ БЕЗ НАС НЕ ЛЕТАЮТ
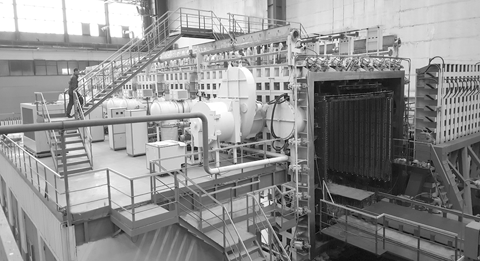
19 августа ПАО «Электромеханика» отмечает 78-ю годовщину
со дня своего образования.
В начале 30-х годов прошлого века в Москве в храме Большого Вознесения (именно там, где в 1831 году А.С. Пушкин венчался с Натальей Гончаровой) разместился один из цехов завода N№ 207. В нем выпускались каркасные цельнометаллические дирижабли и глиссеры. На базе этого цеха 19 августа 1939 года открылись экспериментальные сварочные мастерские Оборонпрома.
В 1939 году перед коллективом из двухсот с небольшим человек стояла задача: разработать сварочное оборудование для оборонной промышленности. И она была успешно решена.
Уже в этом году на предприятии была изготовлена из пластин нержавеющей стали 23-метровая фигура рабочего для международной выставки в Нью-Йорке.
В первые месяцы войны завод был эвакуирован в Кемерово, а 12 июня 1945 года Совнарком принял решение о перебазировании завода в Ржев — с этого момента предприятие вело свою расширяющуюся деятельность здесь. В июне 1962 года на нем провели первое титановое литье и было поручено изготовление оборудования для производства высококачественных литых деталей из титана для одного из авиазаводов, где создавался первый отечественный сверхзвуковой лайнер Ту-144.
Союз науки и производства всегда приносил хорошие результаты. Коллектив предприятия участвовал в работе по подготовке и запуску первого искусственного спутника Земли, космического корабля «Буран». С 1974 года завод п/я 80 был преобразован в производственное объединение «Электромеханика». С 1995 года генеральным директором стал Виктор Константинов.
Сегодня ПАО «Электромеханика» — это сложный научно-производственный комплекс. Современное оборудование для производства деталей, изготовленное нашим предприятием, применяется на всех двигателестроительных гигантах РФ: «Салют», «УМПО», НПО «Сатурн», «ПМЗ» (Пермь) — там создаются газотурбинные двигатели для авиационной, сухопутной и морской техники. «Электромеханика» участвует в проектах Объединенной двигателестроительной корпорации по созданию авиадвигателей поколения «четыре плюс» и пятого поколения.
Девиз «Без нас самолеты не летают» напрямую отражает профиль ПАО «Электромеханика»: производство станков и оборудования для авиастроения. Последний значимый проект, реализованный в течение года, особенно ярко подчеркнул возможности «Электромеханики» — это реконструкция вакуумной печи «УВН-45-180/8,5» для отжига и обезводораживания сварных конструкций фюзеляжа ракетоносца Ту-160 («Белый лебедь»). Эта огромная работа проводилась в рамках модернизации и оснащения Казанского авиазавода современным оборудованием и технологиями по программе производства Ту-160-М2.
Стоит отметить общие габариты этой установки — 68х24 х9,2 метра, габариты рабочего пространства (внутренние габариты печи) — 23х4,2х4 метра. Рабочая температура — до 900 градусов. Масса загружаемых изделий — до 15 тонн! Данные параметры необходимы для загрузки фюзеляжа самолета целиком, то есть позволяют производить обработку не отдельных узлов, а всей основной конструкции уже после сварки.
Первым шагом мы выполнили разработку конструкторской документации на восстановление и модернизацию установки «УВН-45-180/8,5», предназначенной для реализации технологической операции отжига титановых изделий, в точном соответствии с требованиями утвержденного Н.С. Гайнуллиным — директором технологического центра КАЗ им. С.П. Горбунова — технического задания, руководствуясь опытом проведения более 450 садок в период с 1981 по 1994 годы.
В первую очередь была проведена дефектация вакуумной печи и гидроиспытания. На основании полученных данных разработана технология для изготовления узлов. Далее производились различные технологические расчеты: тепловой, электрической, вакуумной системы и другие. Практически все узлы печи, кроме непосредственно самой вакуумной камеры, подлежали изготовлению вновь в соответствии с современными стандартами качества.
Одной из важнейших задач модернизации было не только сохранение паспортных данных, но и придание установке новых технологических возможностей, существенное снижение энергозатрат.
Для снижения потребляемой мощности печи с 9 до 6 МВт были разработаны новые конструктивные решения, введены дополнительные элементы многослойной экранной защиты по результатам эксплуатации печи.
Для реализации технологического процесса отжига титановых изделий обеспечено равномерное температурное поле (отклонения не более 3 градусов) по всему объёму рабочей камеры установки. Система нагрева состоит из 62 зон, равномерно распределённых в камере.
Увеличена производительность получения рабочего вакуума за счёт оснащения печи унифицированными территориально распределёнными низко- и высоковакуумными станциями на базе современных золотниковых, роторных, диффузионных и геттерных электродуговых насосов. Установлено 14 низковакуумных станций, 14 высоковакуумных станций на базе диффузионных насосов, 4 высоковакуумных станций на базе геттерных насосов. Вакуумные станции объединены по цифровой сети с автоматизированным рабочим местом оператора. Данный принцип построения вакуумной системы позволил обеспечить в камере вакуум до шестой степени!
Система водяного охлаждения на базе сухих градирен состоит из независимых контуров: рабочая камера, вакуумная система, система нагрева. В комплекте предусмотрена резервная система подачи воды при аварийном отключении электроэнергии. Установка оснащена дизельным генератором для обеспечения надёжного охлаждения всех теплонагруженных узлов установки в случае нарушения энергоснабжения.
Разработанная новая система управления установки «УВН-45-180/8,5», построенная на базе ПЛК-архитектуры, обеспечивает проведение термической обработки в автоматическом режиме по заданной схеме технологического процесса с возможностью корректировки параметров процесса в реальном времени.
Таким образом, программно-аппаратные средства системы управления открывают широкие возможности по совершенствованию и дальнейшему развитию технологии вакуумного отжига титановых изделий.
Для управления техническим процессом установка УВН оснащена отдельным операторским помещением, где интегрировано управление всей установкой, визуализация всех механизмов, показаний датчиков давления и температуры от всех стационарных термопар.
Проведен большой комплекс испытаний, которые показали значительно лучшие результаты, чем того требовало техническое задание. Ряд примененных технологических процессов стали открытием не только для персонала, который будет эксплуатировать оборудование, но и для ведущих научных учреждений РФ. В настоящее время проводится обработка не испытательных образцов, а готовых «боевых» изделий. Установка полностью готова к промышленной эксплуатации, а «Электромеханика» — к новым проектам.