Технологии, точность, качество
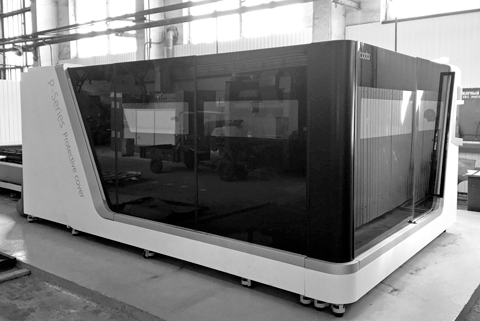
В одном из недавних номеров газеты мы рассказали об итогах и планах ПАО «Электромеханика». Среди прочего звучали такие факты: общий объем инвестиций в объекты производственного назначения составил порядка 177-ми миллионов рублей, идет крупная модернизация механического и заготовительного участков, приобретается новейшее оборудование, предназначенное для лазерной и гидроабразивной резки металла, новые расточные комплексы и обрабатывающие центры. Кроме этого, готовится новый участок для порошковой металлургии и аддитивных технологий. Об этом мы еще обязательно расскажем, и не однажды: руководство публичного акционерного общества «Электромеханика» уделяет большое внимание обновлению и модернизации оборудования, способствующего росту производительности, улучшению качества выпускаемой продукции и условий труда работников.
В 2017 году были приобретены две установки гидроабразивной и газоплазменной резки, которые установлены и работают в сварочно-сборочном производстве. На механическом участке среди прочего оборудования теперь есть обрабатывающий центр «WMC-1600» для фрезерной обработки, горизонтально-расточной станок с ЧПУ «HBM-4 «Челленджер», для сборочного производства электромеханический листогибочный пресс «PRIMA POWER eP-1030». Основным направлением работы «Электромеханики» было и остается производство уникального высокотехнологичного оборудования по заказу предприятий двигателестроительного и авиакосмического комплекса. Это единичные проекты больших размеров и сложности, разработанные специально под техническое задание каждого конкретного заказчика. Но наряду с этим «Электромеханика» развивает и другое производство. Новое оборудование позволяет расширить номенклатуру выпускаемых изделий именно серийного назначения и делать то, что всегда востребовано: металлические шкафы для электрооборудования и медицинских препаратов, инструментов, стеллажи для документов, пожарные ящики… Словом, наладить выпуск продукции самого широкого назначения.
А о характеристиках и возможностях новых установок мы беседуем с заместителем главного механика Игорем Столбовым.
— В этом, 2018, году для механического производства мы закупили еще три станка с ЧПУ — два токарных BNC26120 и BNC1860, и горизонтально-расточной станок «HBM-4 «Челленджер» (малый обрабатывающий центр, аналогичный приобретенному в прошлом году, только с меньшим размером стола), — рассказывает Игорь Олегович. — В конце февраля-начале марта мы побывали в Санкт-Петербурге, в Балтийской промышленной компании, где прошли испытания на холостом ходу всех трех закупленных нами станков. Сейчас в механическом производстве завершаются их установка на фундамент и пуско-наладочные работы.
Модели приобретенных токарных станков позволяют обрабатывать детали (в том числе и тела вращения) сложной конфигурации с высокой точностью и чистотой поверхности. Длина обрабатываемых на станке BNC26120 достигает до 3000 мм, на станке BNC1860 — до 1500 мм.
Что важно: данные станки предполагают минимальное участие человека, что дает возможность одному оператору обслуживать одновременно несколько станков.
Горизонтально-расточной станок «HBM-4 «Челленджер» предназначен для расточки объемных корпусных изделий. Размеры рабочего стола станка — 1200 мм х 1500 мм. Максимальная нагрузка на рабочую зону стола — 5 тонн. К тому же, еще он — поворотный, что позволяет за одну операцию обработать все четыре поверхности или четыре грани изделия. Обработка корпусных деталей, канавок под уплотнения проводится с высокой точностью и высоким качеством обработки поверхностей, что обеспечивает необходимую герметичность.
Для этого станка мы приобрели еще и многофункциональную фрезерную головку, так что, кроме расточки, он может производить фрезерные работы, а также работы по нарезке резьбы и отпайке.
В сборочном производстве запущена в работу установка лазерной резки «Bodor».
Лазерная резка является одним из методов тепловой резки. Это современный процесс, широко используемый в обработке материалов. Лазерная технология применяется для резки различных материалов, в том числе и композиционных, неметаллических листов и обеспечивает высокую скорость резки и высокое качество по сравнению с другими методами резки.
Лазерная резка производится с помощью сфокусированного лазерного луча с высокой плотностью энергии, который действует как режущий инструмент, в то время как высокоскоростной поток вспомогательного газа с той же осью, что и луч света, удаляет расплавленный металл. Хорошее качество резки обеспечивается благодаря небольшому лазерному пятну, высокой плотности и высокой скорости резания.
Начальник участка СП Евгений Викторович Сафронов рассказывает:
— Установка лазерной резки «Bodor» осуществляет раскрой листового материала (нержавеющей стали, цветных металлов) толщиной до 4 мм, алюминия и меди — до 3 мм, углеродистой стали — до 10 мм.
Установка имеет два сменных рабочих стола, находящихся друг над другом и работающих одновременно. Один стол находится в рабочей зоне лазера и на нем производится раскрой металла, на втором в это же время проводится загрузка или, наоборот, выгрузка материала, что обеспечивает непрерывную работу установки. Ее нормативное время работы — 24 часа в сутки.
Обслуживает установку лазерной резки «Bodor» оператор Александр Воробьев. Познакомимся и с ним.
Александр — еще совсем молодой человек. Родился в 1993 году в Ржеве. Закончив среднюю школу, поступил в Московский институт инженеров транспорта. С 3-го курса был призван в армию. Служить довелось в танковых войсках, сначала во Владимире, потом в Калуге.
Отслужив, вчерашний солдат вернулся в родной Ржев, устроился на работу в путевую машинную станцию Октябрьской дирекции по ремонту пути, а немного позднее в Ржевском колледже им. Н.В. Петровского обучился профессии электрогазосварщика.
На «Электромеханику» Александр Воробьев пришел в апреле 2016 года. Сначала трудился электрогазосварщиком 3 разряда, а уже в июле перевелся в сборочное производство оператором станков с ЧПУ 2 разряда. Через полгода сдал уже на 3-й разряд. Опыт у Александра еще невелик, он нарабатывается с годами. Но у него есть самое главное — желание работать, тем более, что работа ему нравится. «Процесс интересный, установка современная. Каждый раз делаешь что-то новое, много разных, новых изделий, скучать не приходится. Работать на таком оборудовании мне особенно нравится!»
Подготовила
Галина ВИНОГРАДОВА